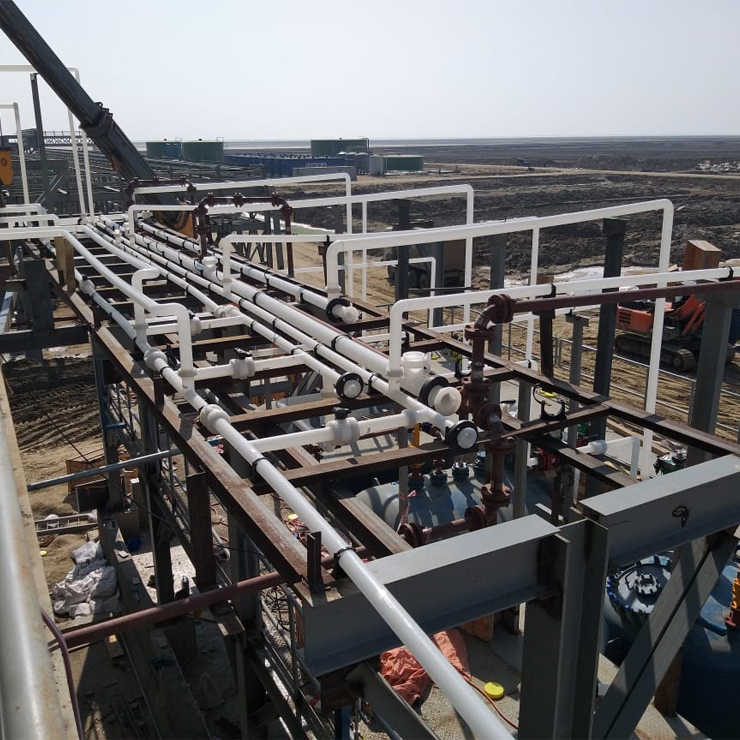
Turnkey Projects
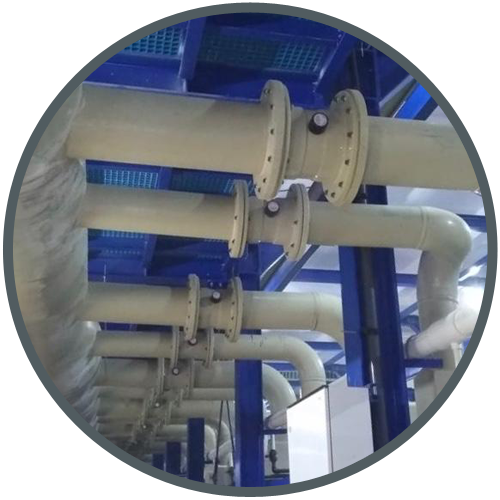
Veza Solutions is well placed to assist its clients in overall Piping project delivery through an end-to-end, turnkey project service suite or selective service offering based on the client and the project requirement.
Veza Solutions project services range from complex site survey to designing; from installation to commissioning. Our rich expertise in successful installations of various Thermoplastics covers an entire gamut of customer requirements across the value chain. Moreover, its global expertise in project execution assures the customer of best-in-class piping solutions delivering high reliability and consistent performance.
Veza Solutions Project Services and Solutions Stand Apart from Others Because of:
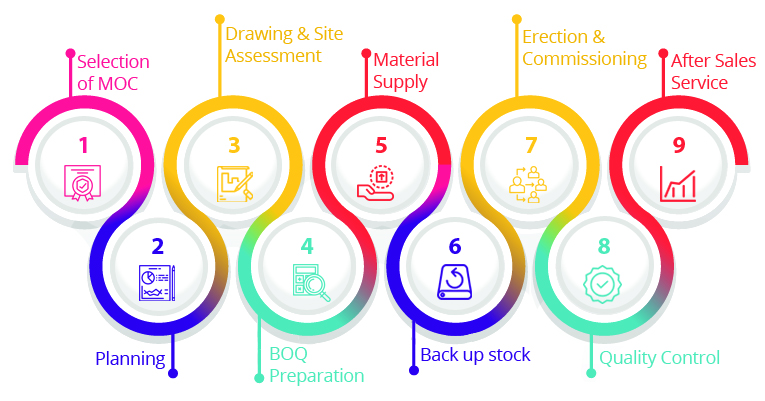
1. Selection of MOC
Veza Solutions has a vast experience in Thermoplastic systems and access to various chemical resistance data software which allows us to provide the most suitable TECHNO-COMMERCIAL solutions to our customer as per their applications and requirements. We guarantee what we supply and install.
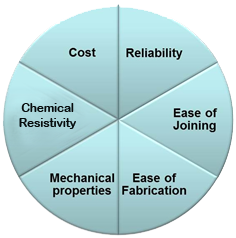
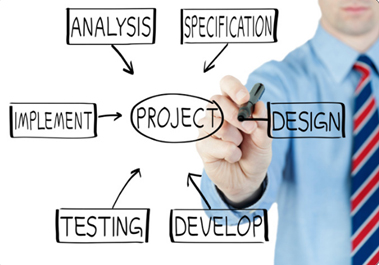
2. Planning
At Veza Solutions we strictly follow PLANNING FUNDAMENTALS. Our team of expert analyse and estimate entire project right from the concept stage, to commissioning and completion of project. We also conduct extensive research that involves mapping customer specific needs and latest market dynamics. The scope of these solutions extends to detailed engineering, vendor sourcing, manufacturing inspection plans, project scheduling, and erection & commissioning of our range.
3. Drawing & Site Assessment
Our Piping experts thoroughly go through the entire GAD, P & ID and Layout drawings to confirm the quantities. Also, a team of supervisor and installer visits site to consider all geographical, climatic and environmental factors into consideration.
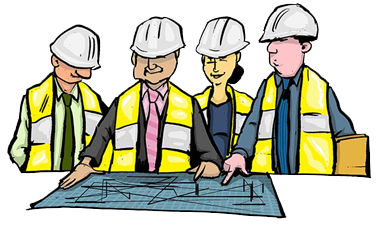
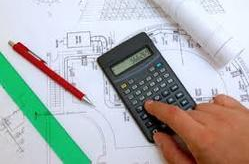
4. BOQ Preparation
Veza Solutions has a strong back up hand which process all the data prepared from Drawings and Site survey. This processed data is than RECONSILLED by expert before preparation of FINAL BOQ.
5. Material Supply
Veza Solutions ensures that entire supply of material is in line with the requirement of the Project and as per the BOQ prepared. Also, during entire project supply-demand data is closely monitored to avoid any shortage of material during the time of project execution.
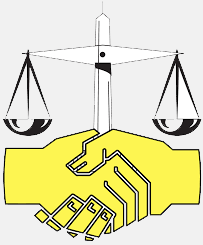
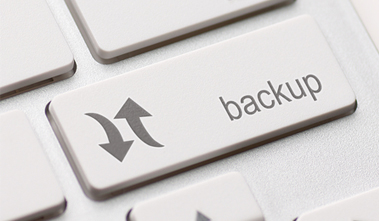
6. Back up stock
We believe in timely execution of project and to achieve that we have to meet on site urgent requirement. To cater the same at our warehouse we maintain an adequate inventory at different locations in India which BACK UP ALL PROJECT URGENT REQUIREMENT and ensures supply of all components at site on time.
7. Erection & Commissioning
We, at VEZA SOLUTIONS strictly follow protocols to provide above standard workmanship, project schedule and safe working practices. We are bind to follow below work practices to deliver Quality work man ship.
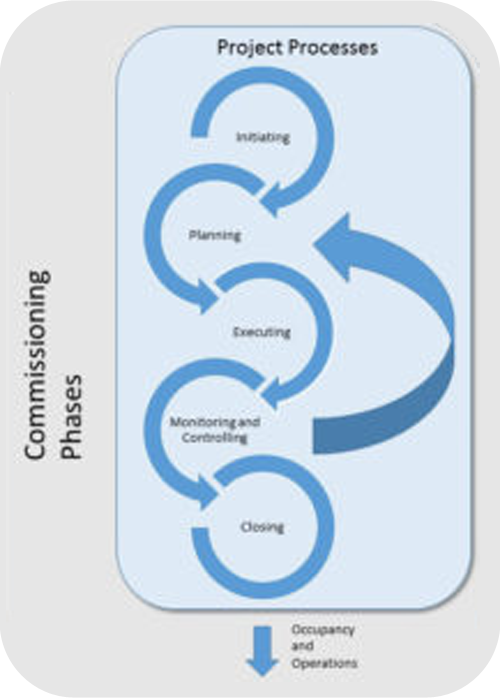
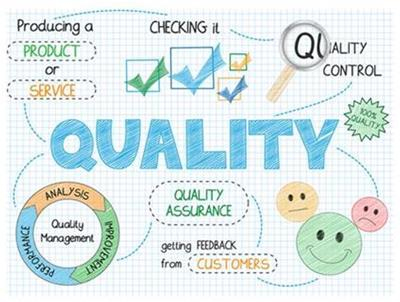
8. Quality Control
VEZA SOLUTIONS firmly believe in delivering Quality. For the same we have Quality inspectors who performs necessary test on finished components and also inspect sourced material and verify documents like Test Certificates, QAP, Country of origin, raw material certificates, etc.,. prior to installation.
9. After Sales service
Our close relationship with our customer does not end once our product and service is delivered — it is only just beginning. Because we strongly believe there are many ways to serve your customers well after a sale by helping them to continually get the most out of your service or product.
We have built trust and loyalty with customer by offering following after sales service.
A. Preventive maintenance and inspection
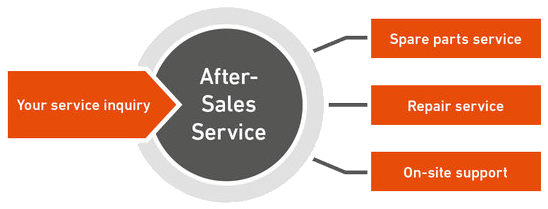
B. Spare/consumable parts and accessories
C. Modification and upgrade
PVDF Installation for Bromine Plant, Plant in Production after successful job completion, In house Automation assembly and testing, Skid mounted System Supplied for TECHNIP FRANCE – A project of UN (United Nations), Thermoplastic Tank Manufacturing at Site, Customized FRP LADDER for SPECIAL APPLICATION at SHIPPING PORT, Thermoplastic Supply & Installation in Food and Pharma industry
View More Projects